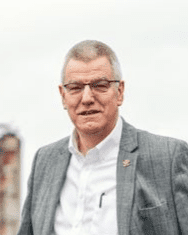
A conversation with Dai Hayward MBE, CEO of Micropore Technologies about Micropore’s cutting-edge technology for the production of monodisperse emulsions and why the technology meets with enthusiasm among customers
EURO COSMETICS: Dai, can you tell us about your background and area of expertise?
Dai Hayward: During my first degree I majored in chemistry, biochemistry, and physiology. My career has always been involved with chemistry for the effects it can produce and so has spanned most of the sectors where the performance of a particular chemistry has been important. This has taken me across many interesting fields in coatings, automotive, nanotechnology, biotechnology and many others.
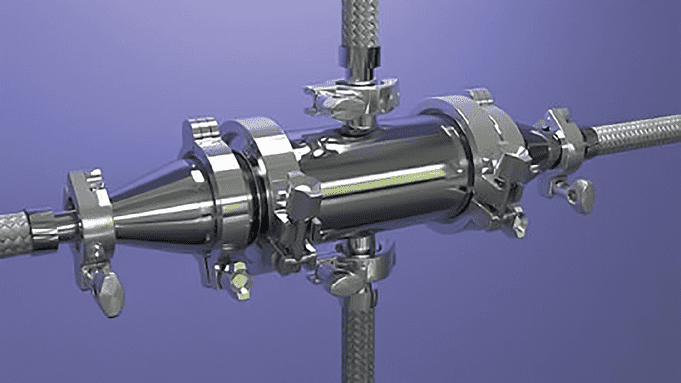
EURO COSMETICS: What makes it special to work for Micropore?
Dai Hayward: We have an extremely capable young team who won’t take no as the answer to any problem. They will work creatively to find the solution to any problem a customer comes with – and, in by far the majority of cases, they succeed. This can-do attitude, coupled with a culture that embraces failure for all the positives it can bring makes Micropore a very special place.
EURO COSMETICS: What can you tell us about Micropore Technologies company
history?
Dai Hayward: Micropore Technologies was founded by Prof Richard Holdich in 2003 when he decided to exploit his research in the field of membrane emulsification.
While the technology offered a lot of promise to many blue chip companies, the problem was how to deliver the technology at industrially meaningful scale – a problem we solved in early 2018.
EURO COSMETICS: Does the collaboration with the university still exist today? And what role does it play for Micropore?
Dai Hayward: Our collaboration with Loughborough University remains strong. We work with a number of researchers there in fields as diverse as precious metal recovery from waste to improved personal care formulations. As an indication of the continuing strength of our relationship, Dr Marijana Dragosavac, has succeeded Richard Holdich as our CSO.
EURO COSMETICS: Can you tell us more about the leading role your company has been playing in the industry?
Dai Hayward: We are currently working with many of the leading fragrance houses, as well as some of the smaller ones, to deliver enhanced performance, such as release control, for their products. In other personal care applications we’re working
to deliver products that are manufactured with zero waste. When combined with the 87% saving in energy we can achieve we see that companies want to collaborate with us to help them achieve their sustainable development goals.
EURO COSMETICS: “There’s nothing on the market that compares to Micropore’s encapsulation technology”. Please explain.
Dai Hayward: Micropore offers a highly engineered solution which offers better products with a much greener footprint and manufacturing scale, from a few kgs to over a thousand tonnes, than any comparative technology. And all this robust technology comes in a very energy and resource efficient small footprint.

EURO COSMETICS: Last year you’ve received the Excellence in Pharma Award for API Development based on your unique technology for Membrane Crystallisation. How important is this award for you personally and your team?
Dai Hayward: Membrane Crystallisation is a development project but it illustrates he breadth of application to which our membrane technology can be applied. It is focused on the final stage of active pharmaceutical ingredients (APIs) manufacturing to improve their consistency and performance while reducing any downstream that is currently used. We’ll have more to say about this in the future.
EURO COSMETICS: Why is it important to you to give your team “more courage to make mistakes”?
Dai Hayward: In my early c areer I was often reprimanded when I made a mistake.
This meant that I didn’t offer any new ideas and simply kept my head down. Here at Micropore we’re constantly pushing the boundaries – and doing so at speed. In doing so we will all make mistakes. I do not want anyone to stop trying because they’re reprimanded for a mistake. Allowance of failure is therefore an embedded feature of Micropore’s culture with one important caveat. We must all learn from failure as we continue push boundaries as we grow.
EURO COSMETICS: How can customers benefit from a collaboration with Micropore?
Dai Hayward: We offer shortened development times with high performance products at optimal cost at the end of a collaborative development programme.
And when the technology is transferred into the client’s manufacturing facility we offer a process guarantee to help reduce the risk.
“Micropore’s technology
is a robustly scalable
technology suitable
for the delivery of
many cosmetic delivery”
EURO COSMETICS: Your unique processing technology is capable of making monodisperse emulsions. Please tell us some about the value you see for cosmetics.
Dai Hayward: To briefly introduce the technology, Micropore’s membrane-based technology uses 316 stainless steel membranes with laser drilled pores with a well-defined diameter and geometry. We then use this membrane to introduce our dispersed phase into our continuous phase. For example if we were to make an oil in water emulsion, we would inject the oil through the membrane, where it would form a droplet at the surface of the pore.
We then use shear force or liquid flow to deform and detach the droplet from the membrane surface. By controlling the injection rate and the amount of shear and, of course, the design of the membrane, it allows us to produce monodisperse emulsions at relatively high phase concentrations and at industrial scales. Until recently, one of the challenges of the technology has been the lower end of the size range. Below about 3 microns, laser drilling starts to bring in a margin of error.
Typically, the rule of thumb is that our droplet size is between 3 and 5 times the pore size, so we have been limited to about 10 microns at the small end of the scale.
We have recently developed a way of reducing this, which allows us to achieve 95% of droplets below 2 microns, this opens up application areas where we have been limited previously. We also have adapted the technology to be able to make nanoscale liposomes for the pharmaceutical industry, more of which later.
While the technology is of interest to our customers their enthusiasm comes from the benefits the technology brings. Let me give you two examples. Firstly, there are the processing benefits, one example is in a significantly reduced energy consumption.
When compared to traditional homogenisation techniques, membrane emulsification uses significantly less energy. For example, a recent study in our labs compared an oil in water system made by homogenisation versus a membrane device.
The homogeniser used 150 Watts compared to the membrane’s 10 Watts – a greater than 90% energy saving. Secondly, because of the way the two fluids are introduced to each other, there is a reduced chance of the system inverting, thus reducing additional processing steps, increasing yields, reducing waste and increasing plant uptime.
Once you’ve made the emulsion there are a variety of post processing chemistries you can utilise to turn the emulsion into various delivery systems. For example, oil and water systems can be processed in such a way as to produce a core-shell microcapsule that will remain stable in a formulation for a long period of time, only releasing the active contents of the core upon application, e.g. rubbing into the
skin. These can be used for delivery of beneficial actives to the skin, vitamins, skin whitening actives, antioxidants, antiacne, fragrance delivery, insect repellents;
basically a whole range of different actives. These systems help preserve sensitive materials from oxidation or the effects of other materials in the formulation.
Equally, water in oil systems can be used to produce hydrogel particles or indeed multiple emulsions including water-in-oilin-water, or oil-in-water-in-oil. These can
allow you to formulate with both hydrophobic and hydrophilic materials contained
within the same particle. This enables the production of some very advanced formulations and work with materials that traditionally have been incompatible for use within the same formulation, so this approach really opens up the formulation space.
EURO COSMETICS: From our experience it has been very difficult to make stable cosmetic emulsions. How does your ability to make them virtually monodisperse help stability?
Dai Hayward: The key advantage of achieving monodispersed emulsions are that, because every droplet is the same size and therefore volume, they all have the same buoyancy. This eliminates the inherent instability of a crude emulsion, such as coalescence, creaming and sedimentation.
Monodispersity thus improves issues such as long-term stability. Also, because of monodispersity sensory qualities are improved, for example skin feel.
We’ve also found, with some formulations, it is possible to reduce the amount of surfactant or emulsifier due to the droplet monodispersity compared to the same formulation being made via traditional homogenisation, providing a further saving on raw material costs. Also, we have some work underway looking at different surfactant blends to try and optimise further.
That said it is not for us to inflict our formulation approaches on our clients, as they know their formulations and we know our technology. One thing we do know is that, by working together, we can optimise both to get the best possible end result for the collaboration.
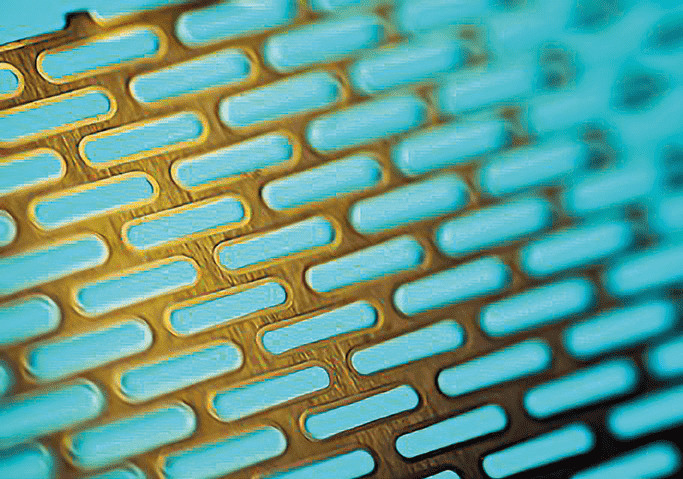
EURO COSMETICS: Dai, it is well known that the combination of dispersed/internal phase and continuous/external phase fluid viscosity is very important. Could you please elaborate on this and explain the advantages of your processing for various fluid viscosities?
Dai Hayward: As a spin off from Loughborough University we have extensive mathematical models to help us predict the behaviour of high viscosity dispersed phases. We have to consider a number of parameters such as the membrane pore size, the number of pores or open area, and then the running conditions such as the injection rate through the membrane and the amount of shear force applied to the surface of the membrane. In addition, we have to consider the viscosity and interfacial tension of the materials we are working with and any surfactant or emulsion stabiliser.
By balancing these factors allows us to work with very low viscosity materials such as fragrance oils but also highly viscous materials such as honey whilst maintaining a low coefficient of variation (% CV).
EURO COSMETICS: You mention that you are able to make hydrogels. This ability is particularly interesting to cosmetic formulators working with very high molecular weight gelled fluids. Please help us understand the success of your process for such fluids.
Dai Hayward: It is important to differentiate here between hydrogel particles and high molecular weight polymers such as carbomer, xanthan or guar gums. We can take various hydrogels and process them in such a way, where we form a water-inoil
emulsion and then solidify the hydrogels according to the relevant chemistry.
For example, taking a solution of sodium alginate forming an emulsion and then exposing it to calcium ions and solidifying the particles through ionic gelation. Other hydrogels can be made in a similar way but for chitosan which is soluble in acidic conditions but precipitates in alkaline conditions or the more straightforward approach of using thermosetting systems such as carrageenan, gelatine or agar.
This allows us to develop delivery systems with well-defined and predictable release
mechanisms with the appropriate chemistry chosen specifically for the application.
Many of these systems can made traditionally via dripping technologies. However, one of the advantages of membrane emulsification is that we don’t have to rely on gravity to detach the droplets from the dripping nozzle, meaning that we can make hydrogel particles smaller than, say 300 microns, also the production rate through a membrane with thousands of pores can be much more efficient then a single dripping nozzle .
“We’re working to deliver
products that are manufactured
with zero waste”
EURO COSMETICS: So how much of your work is on regular emulsions, versus the delivery systems, such as microcapsules and microparticles?
Dai Hayward: Until recently the bulk of the work has been on delivery systems, the recent development I mentioned earlier, that allows us to produce a smaller sized emulsion droplets obviously opens up more application areas for traditional emulsions.
Recent activity has highlighted to us the ability to use membranes not just for emulsification but also as an effective micro mixer. We have been experimenting with the manufacture of delivery systems they are not emulsion based, like water-water systems, mixing miscible fluids. This led us to some exciting developments, looking at the mechanism of crystallisation injecting dissolved crystalline actives in a solvent through the membrane into an anti-solvent and looking at the effect of
micro mixing on the crystals size and morphology.
This could be really promising for development of new ways of manufacturing Pharmaceuticals where currently drugs are made through traditional crystallisation methods and then post processed, grinding, jet milling etc. to achieve the ideal particle size for enhanced bioavailability.
In theory we can remove the need for the post processing by forming the crystal the right size and shape the first time by utilising membrane micro-mixing.
Additionally, we have been focusing on formation of phospholipids which self-assemble to form liposomes or lipid nano particles. These delivery systems have had a lot of attention recently due to their use in some of the covid vaccines. We have proved that by using the ethanol injection method we can easily form liposomes or lipid nano particles at scale in a predictable and reproducible manner. We are working with the University of Strathclyde to further develop and characterise this exciting new application area. We know that we can make unloaded liposomes and we are currently evaluating loading strategies and have seen some really interesting results using poly A as a placeholder for mRNA. Liposomes have been this subject of much interest in the personal care formulation
space in the past, so we are excited to consider the possibilities thought these knew capabilities bring.
EURO COSMETICS: Finally, from a technical view you have announced you can make biodegradable monodisperse emulsions.
This will encourage a lot of Formulators as the search for biodegradable cosmetics had increased exponentially in the consumer market. Please tell us about what some of these biodegradable polymers are that can be utilized in your process by cosmetic formulators.
Dai Hayward: I have mentioned a few of them throughout this interview. There are increasing regulatory pressures on some traditional technologies. For example the amino plastic polymeric microcapsules commonly used for some fragrance delivery applications. More and more people are approaching us for biodegradable approaches.
Some alternatives are well known such as complex coacervation made using gelatine and gum Arabic.
Whilst biodegradable, some people are not keen on the use of animal derived raw materials.
We can offer non-animal derived solutions using materials such as chitosan obtained from a variety of sources or the hydrogels I referred to earlier … alginate, chitosan, carrageenan, agar or naturally derived hydrophobic systems based on natural fats or waxes.
Overall Micropore’s technology is a robustly scalable technology suitable for the delivery of many cosmetic delivery systems, including those that are amongst the most challenging. One of our customers has described it as “a true workhorse technology … it just works”. And that’s precisely what we set out to deliver to our customers so they can put their creativity to best use to develop new products are their markets change and evolve.
EURO COSMETICS: And what are the challenges to to achieve high-quality formulations at low prices?
Dai Hayward: I prefer to talk about best value prices because each customer has different requirements. Suffice it to say that Micropore’s technology is sufficiently adaptable to be able to cater for the most stringent requirements of the pharmaceutical industry while also being applicable to very large, cost-conscious bulk markets in food and household products. Underpinning all our work is the need for formulated products to perform against market needs while constantly “doing more with less”. Micropore’s technology guarantees to deliver this in all its chosen markets while helping clients to meet their own sustainability goals.
EURO COSMETICS: Thank you for the conversation